What is the History of Onyx Imaging?
Humble Beginnings
Onyx Imaging was founded in Tulsa, Oklahoma, in 1991 by Lee & Jean Nicklas. At the time, most businesses were using Impact Printers, also known as Dot-Matrix printers. These printers used Ribbons to transfer images onto the paper. Lee & Jean Nicklas have always had a mind for conservation. They forged Onyx Imaging in an effort to remanufacture these ribbon cartridges for businesses all over North-Eastern Oklahoma. Not only was this a way to save businesses money, but by reusing the plastic casings, it also helped to reduce the amount of waste dumped into our landfills. They purchased a Branson 814 sonic welder manufactured by Sonic Power Company and set up shop in their garage. This was our humble beginning.
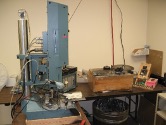
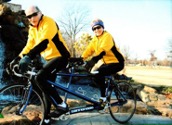
Our Commitment to Quality
As the demand for quality remanufactured ribbons grew, so did the business. When companies began shifting from the use of ribbons to laser printers, ONYX Imaging started remanufacturing toner cartridges as well. There were other companies at the time that also started to refill toner cartridges using “drill & fill” methods. That process did not produce the quality standards that ONYX Imaging’s customers had come to expect. There are still some companies today that continue to use those old “drill & fill” methods. This process refers to when a cartridge is emptied of the old “waste toner” by using a drill to create a small hole and remove the spent toner. Once the waste toner is removed, it is refilled without changing any of the internal parts. This results in poor quality prints and premature failure of the cartridge.
Onyx Imaging knew there was a better way, and it became our mission to produce a product that rivaled the OEM (Original Equipment Manufacturer’s) supplies. Many critical internal parts must be changed to ensure the quality of the cartridge. Most toner cartridges include the following internal critical parts.
- Mag Roller – This is a magnetic roller that picks up the new toner from the toner hopper and transfers it onto the OPC Drum.
- Doctor Blade – The doctor blade controls the amount of toner that is transferred from the toner hopper onto the mag roller sleeve. Too much pressure can cause toner starvation, resulting in light prints. Any scratches or grooves on this component can also transfer issues onto the Mag Roller resulting in various printing defects.
- Retaining Blade – This blade is located behind the mag roller sleeve and helps move the unused toner back into the toner hopper.
- PCR – Also known as the Primary Charge Roller. This roller controls the charge being applied to the drum. An excessively worn or damaged PCR can result in defects ranging from “ghosting” or repeating images, random dots on the print pages, or vertical lines.
- OPC Drum – This component holds the image to be transferred onto the paper. Defects in this critical component can result in pin-hole type dots that repeat evenly down the page, or gray smudges that repeat on either side of the page. The latter indicates an overly worn drum unit.
- Wiper Blade – This component sits next to the OPC Drum. Once the image is transferred from the OPC Drum to the paper, there is excess toner that needs to be removed before the next drum revolution. The wiper blade removes that excess toner and directs it into the waste hopper. One of the most common defects you see if this critical component is not replaced is a thin line printed vertically down the page, or a gray page with visible toner left on the OPC drum.
As you can see, all of these parts work in tandem. So, it is essential that each component is replaced to maintain the integrity of the cartridge. Of course, it costs more to remanufacture this way. But, at ONYX Imaging, quality has always been more important than profit.
One of the most critical parts of our process was the ability to test every single cartridge that we produce. In the early days, we invested thousands of dollars in what is known as an LT-777 test machine. This machine had various plates that you could attach for different cartridge types. In those days, there were only a few different cartridge types being released per year. So, when a new cartridge was released, you could order the adapter plate for the LT-777 machine. The LT-777 is truly a relic of its time. Things have certainly changed since those days! There are now hundreds of cartridges being released by various manufacturers every year. We still test every cartridge we remanufacture. We now purchase a test printer for every cartridge we remanufacture. This helps to ensure it passes our quality control inspection and printing standards. Each cartridge remanufactured by Onyx Imaging is built to the same specifications as the OEM supply.
As our industry has changed, most office supply dealers and resellers have started selling ink & toner cartridges that are manufactured overseas. We decided to keep our manufacturing here. When you outsource your products to large overseas corporations, of course, you lose control over the quality of the product that you offer. Additionally, local jobs suffer. ONYX was built on quality, so letting go of our in-house manufacturing was never an option. We also feel a great commitment to our community by providing local jobs.
Your One-Stop-Shop
The next natural step in our business was to start offering on-site service for printers. By this time, we had a full staff, including two engineers with the experience and knowledge to deliver top-notch service. We started providing service for all major brands and continue that today.
As our customers came to know and trust the products & services that ONYX provided, we began to get requests for office supplies as well. A comment we often heard was, “I wish you guys could supply us with EVERYTHING, and not just our toner.” So that is exactly what we did! We are now a One-Stop-Shop, providing the best products and service at the best price!